DGC’s Rotary Kiln & Rotary Vessel Services include the installation of a new plant, rebuilds, and the planning, scheduling, and consulting for shutdowns and major works on all types of rotary vessels including kilns, dryers, coolers, calciners, ball mills, and rod mills.
Mechanical condition inspections and reports with recommendations for rectifying identified problems are also offered. Our precision onsite and offsite services coupled with our flexibility towards customers’ unique needs allow for significant reductions in equipment downtime.
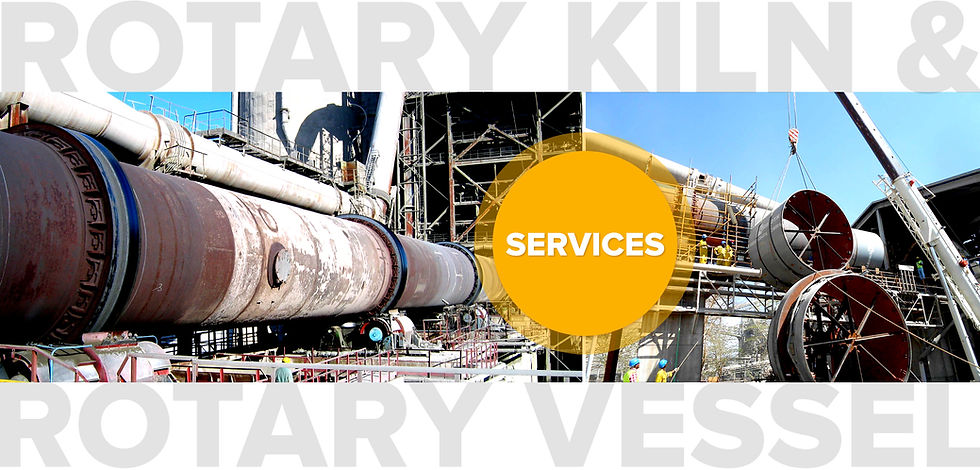
Our Hot Kiln Alignment Services in association with our Routine Inspection Services are tailored to increase plant availability, reduce maintenance-related costs and provide more optimal plant efficiency.
DGC has established a strategic alliance with GEOSERVEX (Poland), for the past 40 years the world leader in the development and implementation of the technology of kiln alignment in dynamic conditions (during normal operation). Geoservex are pioneers of the hot kiln alignment method and a worldwide leader of this service in the global market.

Most problems associated with rotary kilns and vessels can be attributed to misalignment. As such, comprehensive hot kiln alignment significantly contributes towards rotary kilns and vessels’ ability to achieve maximum efficiency throughout their service life, whilst eliminating unforeseen breakdowns.
Some of the consequences of not timeously doing routine or planned alignment are summarised below:
Plant operating outside optimal conditions.
Excessive and unnecessary forces on the vessel/kiln shell.
Metal fatigue and cracking of tyre and shell.
Deformation of vessel/kiln.
Excessive stress on tyres and rollers.
Undue wear on tyres and rollers.
Unnecessary loads on the drive mechanism.
Damage to end seals.
Premature bearing failure.
Frequent premature failure on the refractory lining.
Kiln alignment has to be carried out during the normal operation of the kiln in order to obtain the most realistic information and data on the condition of the kiln without disturbing the clinker production. As a part of preventative maintenance, kiln alignment identifies the actual cause of problems and provides recommendations for appropriate solutions. Our alignment approach is based on advanced measuring techniques and customised hardware and software. It is evaluated by experienced alignment specialists. Based on our experience and considering the major root causes of all kiln failures, our alignment method aims to improve and ensure kiln availability by optimization of Kiln Axis, Kiln Shell Ovality, Kiln Crank and Kiln Axial Balance. For a detailed scope of our services, visit our website - Rotary Kiln & Rotary Vessel Services
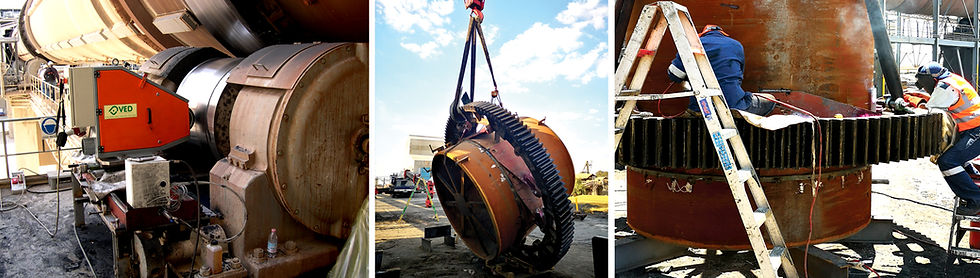
SUPERVISION & TROUBLESHOOTING SERVICES
DGC is well placed with specialists who can deal with most of the key mining, cement, steel, and fertilizer plant’s rotary kilns and rotating vessels.
We can provide technical guidance and assistance for troubleshooting, overhaul, repair, maintenance, and operation of ATOX VRM, Grate Coolers, Kiln, and Ball Mills.
If you have a problem in your kiln, mill, high vibrations in mill/kill drive, problem in grate coolers, or would like to undertake mechanical repairs during your shutdown, you may consult us and employ our trouble-free supervision services.
When supervision and troubleshooting services are carried out by DGC, our specialist will provide all service protocols related to the jobs performed as well as the recommendations for spare parts.
The service protocols are an essential document to ensure the equipment was installed within the allowed limit or not, and root causes for the same if not achieved. Also, this document helps the maintenance department to track activities performed on particular equipment while doing troubleshooting services.

RESURFACING OF TYRE & SUPPORT ROLLERS
DGC provides Resurfacing of Tyre & Supporting Rollers (RTAR) services for all our esteemed rotary kiln and rotary vessel customers. We have specifically designed machines to accommodate and be suitable for various OEMs of rotating vessels including different dimensions of tyre and rollers. All work is completed by experienced DGC’s Grinding specialists. When DGC conducts in-situ grinding of tyre and support rollers, no kiln downtime is needed and our company employs internationally trained grinding engineers to undertake the work. Our grinding engineers constantly monitor axial thrust and bearing temperature throughout the grinding process, carrying out roller adjustments that were required to stabilize axial movement and temperature.
Benefits of Resurfacing of Tyre & Supporting Rollers (RTAR) services:
Reduce the power consumption of the drive station.
Improves the mechanical stability of rotary kiln and rotating equipment.
Improve the contact between tyre and rollers.
Eliminate vibration at the supports.
Reduces zero downtime.
Support roller adjustment for skew correction.
Improves the axial balancing of kiln.
Plant operation is uninterrupted.
Minimize the operating cost.
Prolong service life.

PARTS & EQUIPMENT
At some point, regardless of how well your kiln has been maintained throughout its life, expensive parts like girth gear, rollers, kiln shell sections, etc. will need to be replaced or repaired. We help you find the most cost-effective solution and schedule to perform the work.
We can supply new machinery and equipment or spare parts to suit your existing machinery including:
New Kilns, Calciners, Dryers or Coolers
Replacement Kiln Tyres & Shell Sections
New Mills & Mill Parts
Kiln Seal Assemblies or Parts
Trunnion Rollers & Bearings
Girth Gears & Pinions & Associated Parts
Slew Bearings & Specialised Bearing
Gearboxes & Parts
Mining Machinery
HOW TO GET IN TOUCH WITH US
Ask a DGC consultant about our Rotary Kiln & Rotary Vessel Services at sales@dgc-africa.com or sales@dgrpint.com
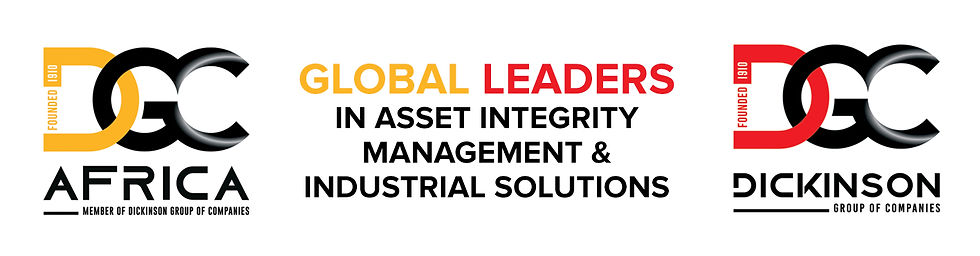
ABOUT OUR COMPANY, HISTORY, AND PARTNERS
Dickinson Group of Companies (DGC) was founded in 1910. For comprehensive information about Our Company – History, Vision & Values, Strategy, Global Alliances, Africa Footprint, Our Commitment to Safety, Anti-Corruption Policy, References, and Industrial Solutions, please visit our website.
