DGC has 36 years of experience as a leader in the design and manufacture of customized precast refractory shapes. With world-class production facilities, engineering, and design technology, the company has the capability to manufacture a wide range of precast shapes for various applications.
The company’s Precast Division was established in 1986, specializing in the manufacture of customized precast refractory shapes. This article gives an overview of some important aspects of this technology.
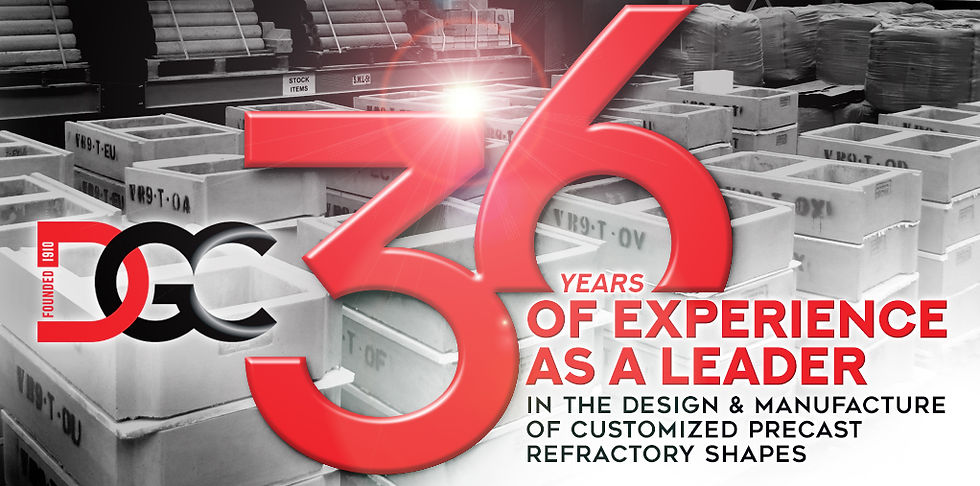
BACKGROUND
Standard refractory bricks are widely used for effective refractory lining in furnaces and their associated equipment. However, where plant geometry, weight limitations and other obstacles do not allow for the use of standard refractory bricks, monolithic refractories are a common substitute. Regrettably, with these mostly being cast onsite, a number of external factors may adversely affect the performance of the resulting refractory lining. Particularly in problematic areas where high rates of wear are observed. Precast refractories address various vulnerabilities that exist within this alternative approach, these custom-made refractory shapes are:
DESIGNED USING 3D PARAMETRIC COMPUTER MODELLING SOFTWARE, MANUFACTURED OFF-SITE UNDER CONTROLLED CONDITIONS AND CURED IN SPECIALLY DESIGNED OVENS. THROUGHOUT THE PRODUCTION PROCESS PRECAST REFRACTORY SHAPES ARE CONTINUOUSLY SUBJECTED TO STRINGENT QUALITY CONTROL MEASURES.
This ensures the manufacture of accurate moulds, final casting and drying of high performance special refractory shapes which enhance the service life of refractory linings. Once manufacturing is complete, the precast refractory blocks are packaged and shipped to clients’ production sites for installations. Their installation is typically a faster and simpler rigging and fitting exercise.

ATTRIBUTES
Our production processes are certified to the ISO 45001 Occupational Health & Safety management system.
Rigorous Quality Analysis and Quality Control processes throughout the production process. The ISO 9001 quality management system is currently being implemented.
Well experienced and skilled teams.
Proximity to other divisions and companies within the group (DGC) allows customers to get complete solutions under one roof. Clients also get access to support in various other aspects of plant maintenance.
Our facilities are specially designed with limited bottlenecks, high production capacities and the ability to handle even large shapes.
Overhead cranes with capacities of up to 20 Ton to assist in the handling of Large Precast Shapes.

PRODUCTION PROCESS
MOULD DESIGN & MANUFACTURE
Polystyrene Moulds
Every component is designed with the latest in 3D parametric computer modelling software and placed into mould assemblies to visually inspect the form and fit of our modules. Once our design and engineering have been reviewed and approved the designs, customers are able to view their final product and how it will be assembled before the component is manufactured. New mould technology has also been introduced using the latest polystyrene and mould designs that employ state-of-the-art technology to produce the highest quality products for our customers.
Wooden Moulds
When needed, the company has advanced pattern making capabilities to design and manufacture highly robust and accurately manufactured long lasting wooden moulds. These reusable wooden moulds are trusted for their longevity. Thorough quality checks are done on the mould prior to use every time.

MIXING & CASTING
The company makes use of a range of high-intensity paddle mixers with capacities to mix from 50kg to 1000kg of material and ensure consistent mixing and elimination of airlocks. Modern adjustable high-frequency vibrating tables are also used when casting large precast blocks.
AIR DRYING & STRIPPING
After casting, the blocks are left to air dry in their moulds for about 24 hours. Thereafter, they are delicately stripped off from the moulds using proper demoulding equipment to avoid any form of damage.

CURING / DRYING
Finally the precast refractory shapes are dried according to their material requirements for this purpose, the company has a range of specialised electric ovens and gas ovens of different sizes that are capable of attaining a range of temperatures up to 450 °C or 1 000 °C. The ovens can be configured to accommodate up to 10 metre lengths of blocks.
DISPATCH
The final products are then properly stacked and packed for delivery to clients’ premises. Our precast refractory shapes are accompanied by all necessary documentation including a Quality Control Pack (QCP) with:
Material certificates,
Heating curves,
Material data sheets and
Drawings.
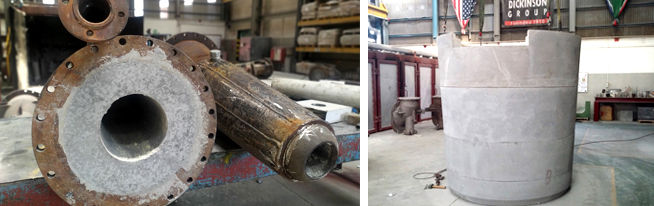
SPECIALISED EQUIPMENT LINING & DRYING
DGC also provides services for offsite lining and drying of specialised furnace equipment linings at the company’s workshops to ensure higher performance of linings.
For such applications, the lining process is very similar to the one described above and is summarised below:
The metallic shell of the equipment to be lined is used as one of the moulds. All necessary preparation is done on this mould including welding of refractory anchors and installation of bitumen painting or anchor caps if required.
Other supporting wooden or polystyrene moulds are also prepared. When required ceramic fibre linings are installed.
Homogenously mixed material is casted, vibrators with pokers are used to ensure even distribution of material.
The new lining is then air-dried. Supporting moulds are removed and curing is done in the ovens. In cases of bigger equipment, external burners may be used for this.
The installation of the units on the client’s production site is a simpler rigging and fitting exercise.
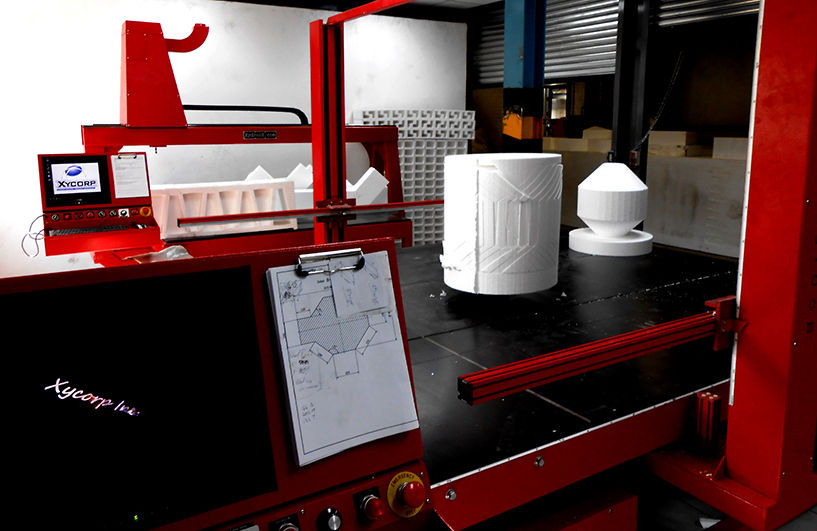
BENEFITS
The revolutionary concept of precast refractory shapes results in numerous benefits including:
Consistent performance and controlled manufacturing process.
Unique purpose developed materials and shapes for each application.
Most work done off-site resulting in minimum interface with production.
Ease of installation and shortened repair times
Enhanced lining service life
Areas of higher wear can be engineered with optimal refractory materials.
Easier slag or dross removal due to lower porosity.
Less down time due to quicker installation and heat-up times are minimized.
Shapes from 1 kg to 9 metric tons, resulting in less joints and faster installation.
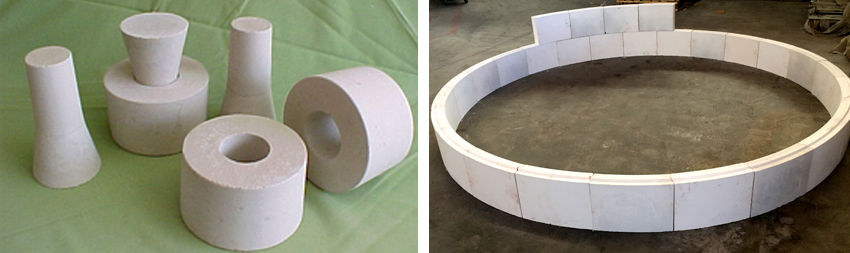
APPLICATIONS
Miscellaneous
Launders
Ladles
Sinter hoods
Shaft kilns
Burners / nozzles
Feed chutes
Combustion chambers
Electric arc furnace roofs
Electrode guides
Sinker bricks
Dampers
Cement Plants
Cooler Bullnose
Kiln Hood
Precast Cyclone Roofs
Burner Pipes
Tertiary Air Duct (TAD) Dampers
Nose Ring Blocks
Calciner Roofs
Cooler Benches
Cooler Roof Sections
