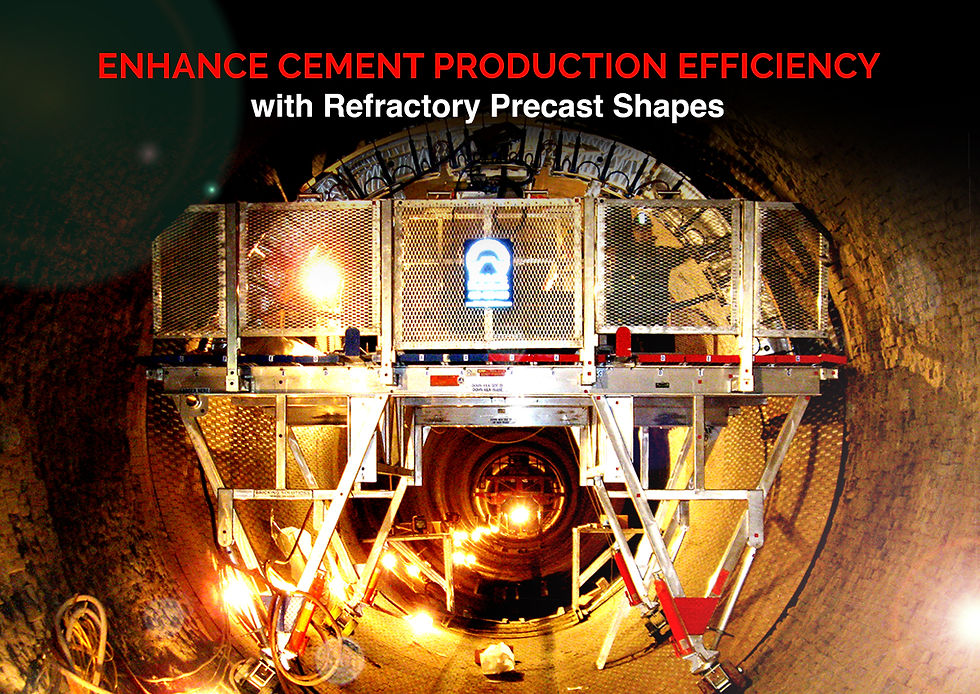
At DGC, we understand the critical role refractory precast shapes play in the cement industry. Our expertise and commitment to excellence enable us to provide tailored solutions that help our customers optimize their cement production processes. We offer a wide range of high-quality, customized refractory precast shapes designed to withstand the extreme conditions of cement manufacturing, from the lining of rotary kilns to preheaters and coolers.
Our experienced team collaborates closely with clients to identify specific requirements, ensuring precise and efficient installations. With DGC, customers can expect superior durability, improved thermal efficiency, and reduced maintenance downtime, all contributing to enhanced productivity in the cement industry. Let us be your partner in achieving excellence in cement production.
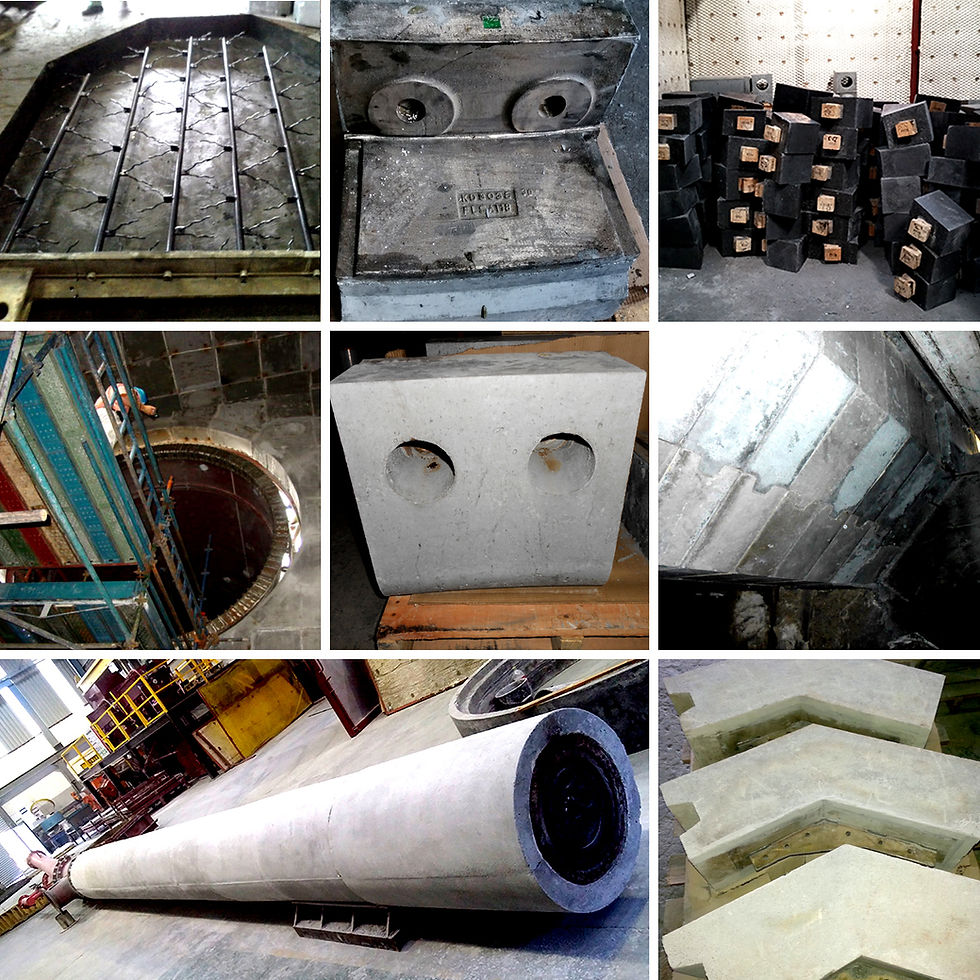
Our facilities are state-of-the-art and fully compliant with Atmospheric Emission Regulations.
Refractory precast shapes are customized, pre-fabricated refractory components used in various industries, including the cement industry. These shapes are manufactured off-site and designed to withstand high temperatures, chemical corrosion, and mechanical stress, making them ideal for lining and protecting the interior of industrial furnaces, kilns, and other high-temperature equipment used in cement production.
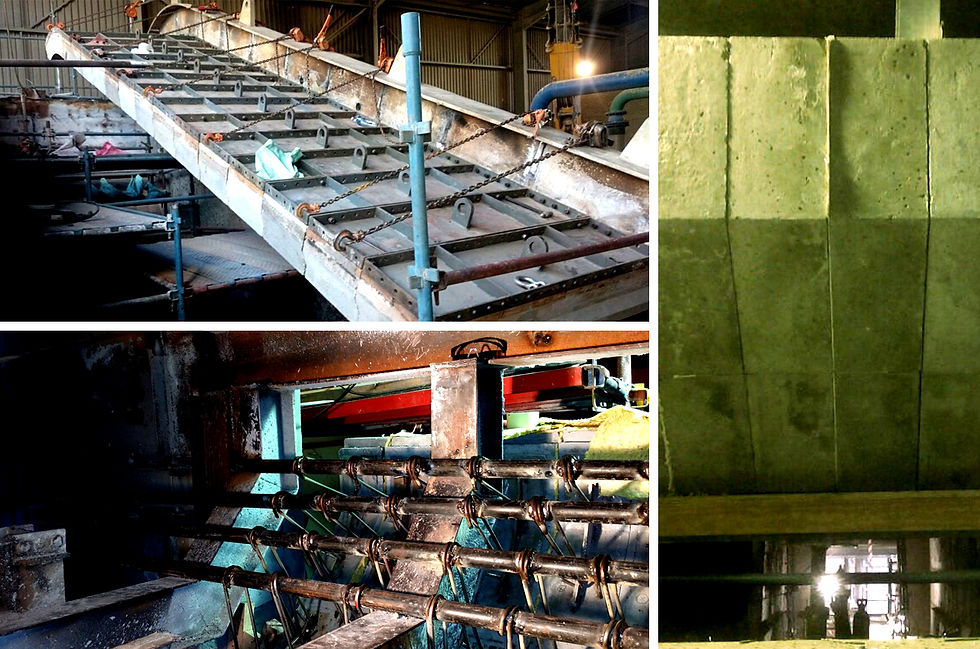
In the cement industry, refractory precast shapes find applications in several key areas:
1. ROTARY KILNS: Rotary kilns are at the heart of cement production, where raw materials are processed at high temperatures. Refractory precast shapes can be used to line the interior of the kiln, protecting it from the extreme heat and chemical reactions involved in clinker production.
2. PREHEATERS AND CYCLONES: Refractory precast shapes are often used in the preheater and cyclone sections of cement plants, where hot gases and raw materials are mixed and processed. These shapes help improve heat retention and protect the structure from wear and tear.
3. COOLERS: In the clinker cooling process, coolers are exposed to high temperatures. Refractory precast shapes can be used to line these coolers, extending their lifespan, and improving thermal efficiency.
4. TERTIARY AIR DUCTS AND BRUNER PIPES: These components are exposed to high-temperature combustion gases. Refractory precast shapes can be used to line these ducts and pipes, ensuring they can withstand harsh conditions and last longer.
5. CYCOLNE DIP TUBES: Cyclone dip tubes are part of the preheater system in cement production. Refractory precast shapes can be used to protect and insulate these critical components from high-temperature gases and abrasive materials.
6. OTHER FURNACE AND KILN LININGS: Beyond the mentioned areas, refractory precast shapes can also be used in various other furnaces and kiln linings within the cement industry to ensure durability and thermal insulation.

These precast shapes are typically made from high-quality refractory materials, such as high-alumina, silica, and magnesite, chosen based on the specific requirements of the application. They are manufactured off-site, under controlled conditions, and can be customized to fit the shape and size requirements of the equipment they are intended to protect. Precast shapes offer several advantages, including faster installation, consistent quality, and reduced downtime during maintenance or repair.
The use of refractory precast shapes is essential in the cement industry to maintain the integrity and efficiency of high-temperature processes and equipment, ultimately contributing to the overall productivity of the cement manufacturing process.
Thank you for choosing DGC
as your trusted furnace service provider.
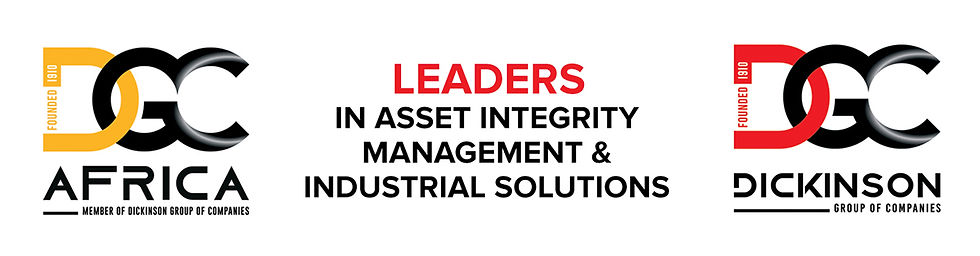
ABOUT OUR COMPANY, HISTORY, AND PARTNERS
Dickinson Group of Companies (DGC) was founded in 1910. For comprehensive information about our company's history, Vision and values, Strategy, Global Alliances, Africa Footprint, Commitment to Safety, Anti-Corruption Policy, References, and Industrial Solutions, please visit our websites.
