
DGC's comprehensive range of industrial linings includes international leaders, Kalenborn International’s wear protection solutions. Kalenborn established 100 years ago, provides protection for the environmental and heavy industries with wear-resistant linings which have excellent abrasion and impact resistance.
The company provides custom design, manufacture, delivery, and installation of its materials to meet customers’ specific abrasion, impact and corrosion problems. This applies in particular to industrial plants handling raw material processing as well as, transport, storage including the processing of ores, sand, slag, coal, or recycled materials.
In this article we will first briefly describe our wear protection materials and then outline some Abrasion & Wear Protection Solutions that are used in different industrial sectors.
WEAR-RESISTANT MATERIALS
We rely on a high-quality range of mineral, ceramic and metallic materials as well as compounds and plastics. That variety enables us to create lining systems that are perfectly matched to each specific application. Our wear resistant materials include the following:
ABRESIST: Wear-proof fused cast basalt for protection against frictional wear KALCOR: Zirconium corundum wear protection resistant to high temperatures and frictional wear KALOCER: Ceramic wear protection for plant components subject to extreme wear and temperature stresses KALSICA: Silicon carbide wear-proof material outstanding against frictional wear in hot conditions KALCERAM: Highly resistant against frictional wear with a low-friction surface which helps items to slide KALPOXY: Compound for the lining of plant components and for repairs, applied by trowel KALEA: Sprayable Polyurea-based wear protection for pipes and plant components KALIMPACT: Hard-material-rubber composite for heavy impact and wear loadings KALCAST: Very hard and wear-resistant chilled iron wear protection for mass-produced components KALMETALL: Welded hard surfacing for high resistance to impacts and wear KALEN: Technical plastic for corrosion-free wear protection which promotes sliding KALDETECT: Wear protection monitoring
INDUSTRIAL APPLICATIONS
Working in close collaboration with our customers, we develop concepts for sustainable solutions and then realize them - both in our own workshops and on-site customers’ facilities. Below is a summary of popular industrial applications as well as highlights from past projects in different industrial sectors:
CEMENT AND BUILDING MATERIALS
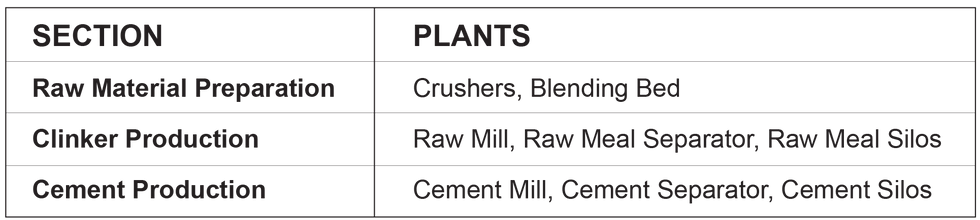
Use Case Overview: CEMENT PLANT
A Canadian Cement Plant was experiencing extreme wear issues on their cyclones. Quench tempered steel linings in six cyclones required patching at an annual cost of $60,000 to $80,000, nearly half of which was allocated to material costs.
Because of quench tempered steel’s disappointing results as a patching material, the plant ordered a lining material made of fused cast basalt, which is resistant to the abrasive effects of clinker and can withstand the cyclone’s 250°C environment. “Since the installation in early 1986,” said the client, “there has been no downtime at any of the six cyclones, and company officials are considering lining eight other cyclones in the same way.”
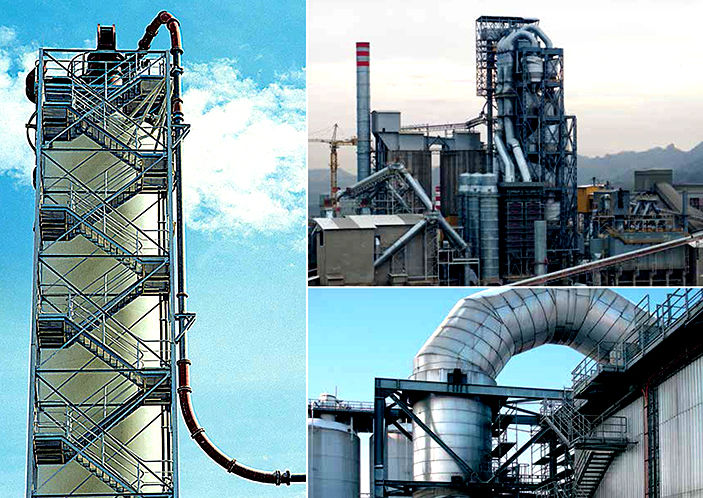
IRON AND STEEL

Use Case Overview: IRON ORE
KALIMPACT helps iron ore flow smoothly at a large Brazilian mine. Previously, the mine’s classifier chute was lined with Hardox 450, but the customer saw continuing wear problems, and the Hardox finish didn’t promote sliding of the material. Working with the customer, Kalenborn engineers recommended KALIMPACT ABR for the application. Since the installation of KALIMPACT, the customer has expressed satisfaction with the resulting performance improvements, as well as the lowered maintenance costs. Thanks to Kalenborn solutions, iron ore nuggets flow smoothly, contributing to productivity and operational efficiency at this exceptional mining operation.

ENERGY & ENVIRONMENT
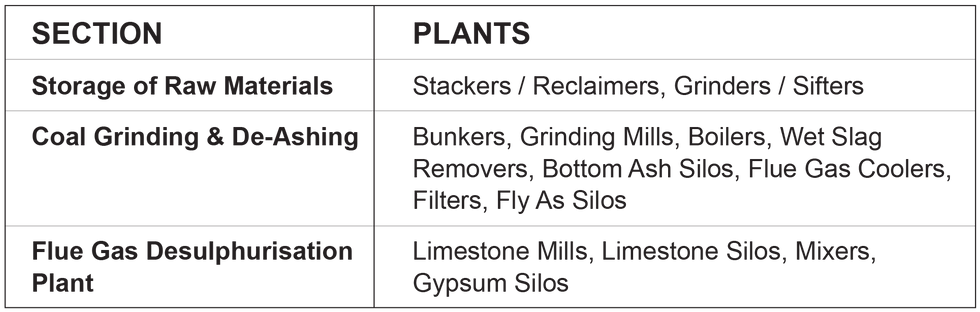
Use Case Overview: POWER PLANT
An American Coal fired Power Plant uses ABRESIST Basalt Lined Steel Pipes to Convey Abrasive Bottom Ash. With a consistency of coarse sand, the bottom ash is extremely abrasive. When the customer installed scrubbers at the plant recently, the bottom ash pipe had to be moved to make room for the new equipment. As workers removed the original basalt pipe they discovered that much of it had withstood 19 years of erosion associated with bottom ash and was reusable. The basalt lined pipe has handled all of the plant’s bottom ash since its construction and is still use.

MINING
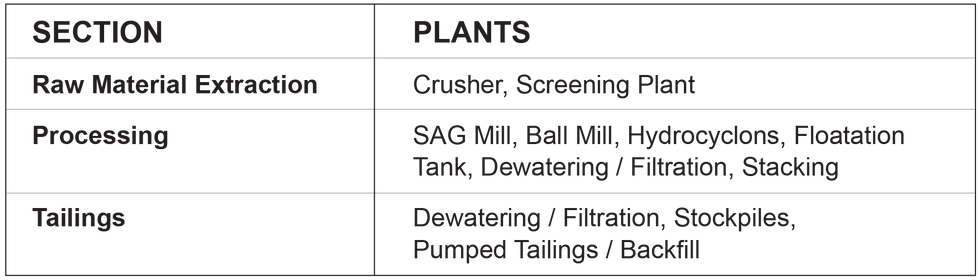
Use Case Overview: COAL
Thousands of feet of pipeline thread coal processing plants. Keeping material flowing through those coal piping lines can be a headache; sharp, abrasive material wear pipelines until they sometimes blow. When they do, production ceases and magnetite is lost. Such was the problem facing a Canadian coal producer.
“When a line or an elbow blew, we had to shut the plant down, and that impacts productivity negatively.” The abrasive coking coal was destroying the mild steel straight pipe and elbows at a startling rate, requiring elbow replacements every six to eight months. Mild steel straights had to be replaced annually.
To solve the problem, the client replaced existing coal pipes and elbows with fused-cast, basalt-lined abrasion-resistant pipes, elbows and fittings manufactured from basalt rock liners, which are molten cast at over 1,300°C and annealed prior to insertion into a steel casing. According to the customer: “using it has curtailed maintenance costs and reduced downtime. We can now plan maintenance.”
Use Case Overview: POTASSIUM SALTS
Potassium salts are mined as rock. It is finely crushed and the crude salt is then enriched with water. The mixture passes through a variety of sieves and other separating devices, which separate the different particles from each other and classify them according on their size and density. To cope with the constant flow of material, the pipe systems of such a plant are protected with ABRESIST. The basalt lining reduces friction in piping and considerably extends its life span. Pipes protected with ABRESIST do not need to be replaced or repaired as often as unprotected piping components. Potassium salt plants in New Mexico and Canada have achieved lifetimes of 20 years or more since Kalenborn Abresist introduced pipes in the mid-1970s.
