
We are pleased to provide you with an update on our recent project involving the demolition and installation of refractory materials in a Rotary Kiln. The project lasted 4 weeks and included the following scope of work:
SCOPE OF WORK
Demolition of Refractory Castable
The project began with the removal of 24 meters of refractory castable material inside the Kiln.
Anchor Replacement
We removed old Stainless Steel Anchors, prepared the shell, and installed new Rotalock Studwelding Kiln Anchors to ensure structural integrity.
Refractory Installation
Following anchor installation, we placed 24 meters of refractory castable inside the Kiln.
Brickwork in Furnace
Brickwork was carried out within the Kiln to optimize its performance.
Water Protection
A wall was cast under the Kiln to protect against water ingress.
Screw Feeder Breakout
The screw feeder was broken out and subsequently cast.
Arch Repair and Anchor Installation
A half-moon arch was installed with Y anchors (LH RH), and two squares were broken out and replaced with VX hand weld anchors, followed by casting.
Dam Wall Casting
The project involved casting the Dam Wall at the Kiln inlet.
Kiln Outlet Arch Brick Repair
We repaired the arch brick at the Kiln outlet to enhance efficiency.
Expansion Box Refractory Repairs
Refractory repairs were carried out in the expansion box at the Kiln inlet.
Dry-out
The final phase of the project involved the dry-out of the newly installed refractory material.

CHALLENGES
Kiln Mobility
The Kiln was immobilized due to the weight of the demolished refractory material at its base, necessitating the use of Brokk machines and manual labour to remove the rubble.
Shell Preparation
The absence of previous shell preparation required the gauging out of old anchors, smoothing the steel shell, and installing new Rotalock Studwelding Kiln Anchors.
Refractory Installation Sequencing
The project's refractory installation sequence had to be adjusted to address challenges related to the Kiln's breakage. This change ensured that Kiln's balance was maintained throughout the process.

ACHIEVEMENTS
Safety First
The project was executed with zero incidents, accidents, or injuries, highlighting our commitment to safety.On-
Time and On-Budget
We successfully completed the project within the scheduled four-week timeframe and adhered to the budget, showcasing our dedication to efficiency and cost-effectiveness.

Stay tuned for more exciting updates and projects as we continue to drive excellence and innovation in the industry.

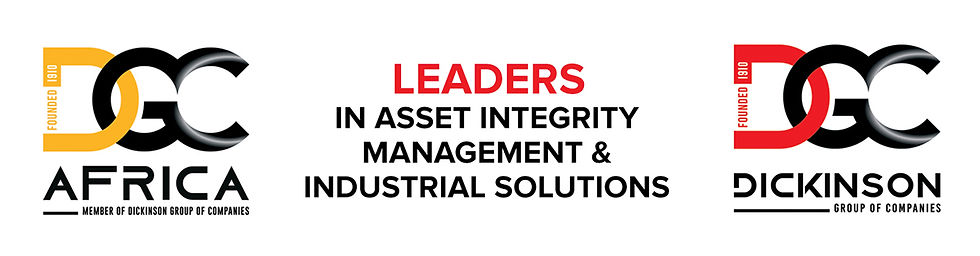
ABOUT OUR COMPANY, HISTORY, AND PARTNERS
Dickinson Group of Companies (DGC) was founded in 1910. For comprehensive information about Our Company – History, Vision & Values, Strategy, Global Alliances, Africa Footprint, Our Commitment to Safety, Anti-Corruption Policy, References, and Industrial Solutions, please visit our websites.
