
DGC is pleased to announce the conclusion of a commercial partnership agreement for the distribution of the complete range of Kalenborn’s Wear and Abrasion Protection Solutions in Southern Africa.
Bringing Kalenborn’s prominent rich tradition characterized by competence and experience as well as durable, quality products to regional players in heavy wear industries. Thereby helping local mines and industrial plants to prevent mechanical wear surface degradation; a challenge that remains a major threat to the longevity and performance of equipment in the heavy industry. This development is part of DGC’s differentiation strategy to open up new market space, to enhance our company’s competitive advantage by - creating uncontested market space, creating and capturing new demand, breaking the value-cost trade-off, and aligning the whole system of the firm’s activities in pursuit of differentiation.
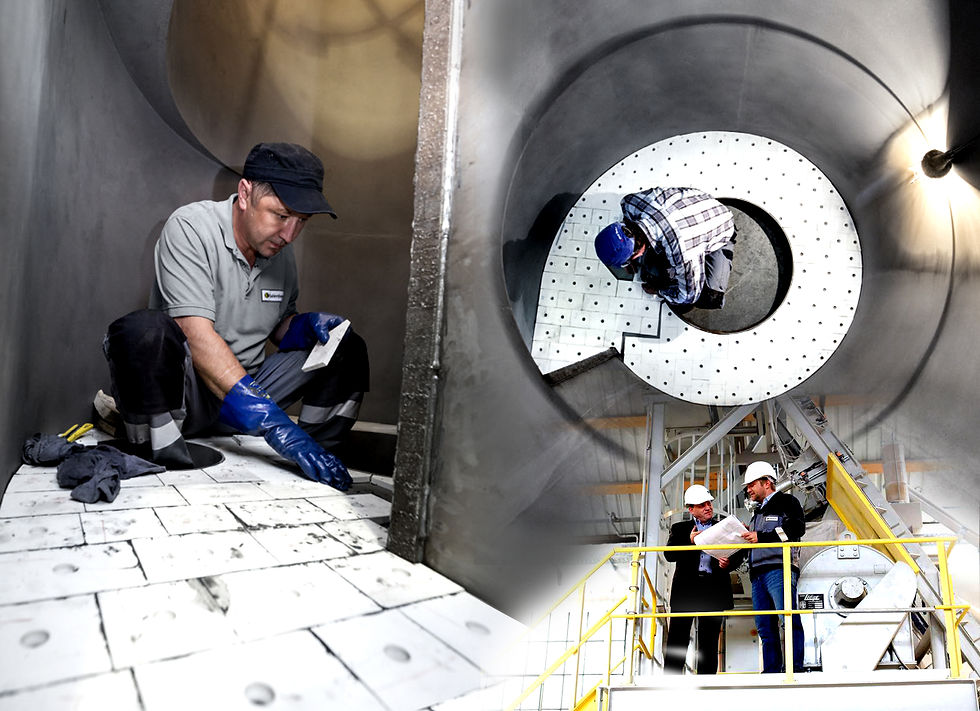
ABOUT OUR PARTNERS

SOUTH AFRICA
DGC has more than 90 years of experience in providing asset integrity management and industrial solutions to the mining, metals smelting, and mineral processing industries throughout the world.
The company undertakes this with a wide range of high quality, niche products and services, which are underpinned with superior technical expertise, delivery performance, and customer service. DGC’s products and services integrate custom made solutions with internationally sourced and market leading technologies. DGC has a dominant presence across sub-Saharan Africa, with offices in South Africa, Zambia and the Democratic Republic of Congo. The company has also successfully completed numerous projects in the region, with extensive project in several countries including: Namibia, Zimbabwe, Mozambique, Tanzania, Kenya, Uganda, Nigeria, Senegal, Egypt, Niger, Malawi and Botswana.

GERMANY
Kalenborn was established over 100 years ago, the company provides protection for the environmental and heavy industries with wear-resistant linings which have excellent abrasion and impact resistance. The company provides custom design, manufacture, delivery, and installation of its materials to meet customers’ specific abrasion, impact and corrosion problems. This applies in particular to industrial plants handling raw material processing as well as, transport, storage including the processing of ores, sand, slag, coal, or recycled materials. Kalenborn has a global network of subsidiaries around the world - Germany, USA, Canada, Brazil, France, Poland, Hungry, Singapore, Philippines, Vietnam and exclusive representation throughout sub-Saharan Africa by DGC.


OUR WEAR AND ABRASION PROTECTION SOLUTIONS
Our wear protection solutions protect industrial plants and equipment reliably against wear due to abrasion and impact. In steelworks and cement plants, in coal-fired power plants and recycling plants, in mining, and in environmental technology, our solutions keep production operations running. From the development of our materials to the lining of pipes, plants, and equipment, we offer a complete range of products and services, all from a single source. In so doing, the quality and durability of our products stand above all else. As experts, we begin with the production of our materials. We know the raw materials and the manufacturing processes. That comprehensive expertise enables us to ensure the quality characteristics of our products at all times.

RANGE OF WEAR-RESISTANT MATERIALS
We produce our wear-resistant materials in our own plants and ensure their quality through material testing in our laboratories in order to find just the right solution for each customer requirement. One of the prerequisites for effective wear protection is also a professional installation, which our employees carry out with special adhesives and fasteners.
ABRESIST: fused cast basalt reliably prevents abrasive wear in plant components such as scale flumes, marl hoppers, fly ash pipelines in coal-fired power plants, and coke bunkers in the iron and steel industry.
KALCOR: a cast ceramic material that is effective for lining plant components that are subject not only to extremely harsh abrasion but also to high temperatures, for example in chutes for hot sinter or clinker, in asphalt mixers and hot gas pipelines.
KALOCER: high-alumina ceramics that are available in thin, smooth moulded elements and are particularly well-suited for lining conveyor belt transfer points, concrete mixers, or cyclones in the food industry.
KALMETALL and KALCAST: armoured plates made of metallic materials. Recommended for protection against the high impact wear typically found in components such as bunker inlets, spiral chutes, and crushers.
KALCRET: hard compound which combines easy handling with excellent wear protection properties under high-temperature loading. To line large surfaces – such as those of separators on a cement mill or of blast furnace dust catchers in an integrated steel mill – the material can be applied without joints using a trowel or sprayed on. Within 48 hours, the plant is ready for operation again.
Very different requirements arise under operating conditions that demand especially good anti-friction properties, e.g., in silos and bunkers. Such applications use not only KALEN, as a thermoplastic material with ideal anti-friction properties, but also the mineral material KALCERAM. They prevent the material which is being conveyed from building up, thereby ensuring uninterrupted material flow.
For rapidly applying a thin, jointless coating to large surfaces or pipes, we offer KALEA, a sprayable material with its own application technology.

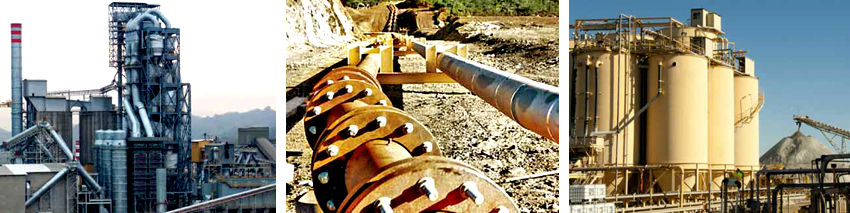
INDUSTRIES
We rely on a high-quality range of mineral, ceramic and metallic materials as well as compounds and plastics. That variety enables us to create lining systems that are perfectly matched to each specific application. Working closely together with our customers is particularly important to us. In close collaboration, we develop concepts for sustainable solutions and then realize them - both in our own workshops and on-site at the facilities of the customer.
Our Wear and Abrasion Protection Solutions cover the following industries: Biomass Power Plants Cement Industry Coal Fired Power Plants Construction Industry Food Processing Industries Insulation Industry Marine Industry Metal Plants Glass Plants Mining Industry Petro Chemical Industry Pulp & Paper Industry Recycling Industry Steel Industry Transport & Bulk Handling Waste to Energy Clay Brick Plants Incineration & Energy