
Mining and Processing operations extract staggering amounts of mineral ores for eventual processing through different refining stages. The associated heavy duty and often continuous loads exert enormous strain on plant equipment surfaces at each processing stage.
Moreover, operations should also handle the increasingly problematic overburden, which as waste material has no value but represents a major factor in the wear of plant components.

DGC in alliance with Kalenborn provide protection for the environmental and heavy industries with wear-resistant linings which have excellent abrasion and impact resistance. The alliance provides custom design, manufacture, delivery, and installation services for its materials to meet customers’ specific abrasion, impact and corrosion problems. This applies in particular to industrial plants handling raw material processing as well as, transport, storage including the processing of ores, sand, slag, coal, or recycled materials.
Numerous mining companies around the world choose our wear protection solutions to help them reduce their operating costs. This article gives a brief overview of our Wear & Abrasion Resistant Linings for Mining and Processing Industries.

EXTRACTION AND MILLING OF RAW MATERIALS In open-cast and underground mining, wear protection linings for loading buckets, lorries and stationary and mobile conveyors represent an important investment in equipment reliability. Our Wear & Abrasion Resistant Linings also provide long-lasting wear protection with feeder chute and housing linings specifically designed for ore and raw materials.
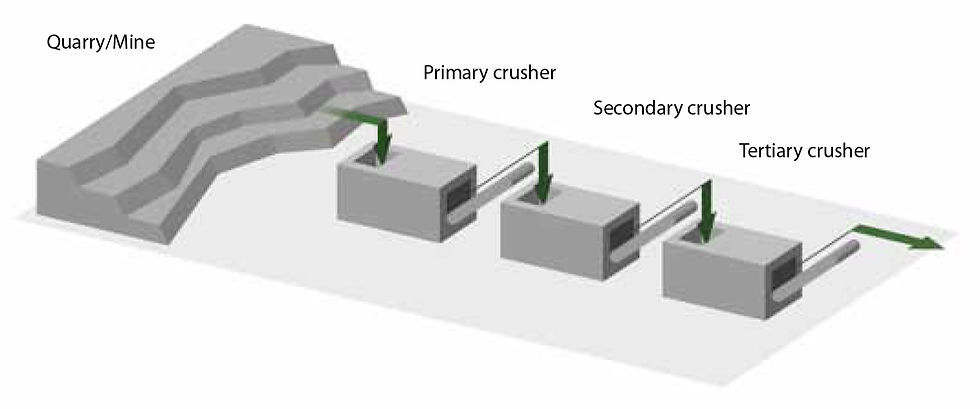
PROCESSING PLANTS
Processes involved in the milling and grading of extracted ores or minerals cause wear in the machinery used for those mining operations, as does the subsequent process of separating the valuable material from the raw stone. Our Wear & Abrasion Resistant Linings protect mills, chutes, hydrocyclones and sorters from the particular stress conditions to which they are exposed in each production process. Wear resistant materials like fused cast basalt and ceramics serve as robust lining materials to protect hydraulic conveyor lines that are used to transport slurries in pumping circuits. Besides mining, our range of customized wear protection solutions are used in other production areas, including operations such as pelletizing and sintering.


WEAR PROTECTION FOR CYCLONES
Along with the hardness of the materials being sorted, flow rate is a major factor that affects wear. In cyclones, particles sometimes reach significant speeds, which cause tremendous wear. Our wear protection linings that are tailored for protecting cyclones are not only strong but also extremely lightweight, in order to add as little as possible to the overall weight of the equipment component.

GRINDING AND CRUSHING
Mills of all types serve as classic examples of wear. No tool used to grind material can escape abrasion over the long term. Mill components which are subject to high wear include not only the rollers and tracks, but also feed units, housings, grit cones, separators and discharges. Our Wear & Abrasion Resistant Linings are successfully used in mills and crushers all over the world – including vertical roller mills as well as horizontal grinding mills and ball mills – where they ensure long service life and economical operation.
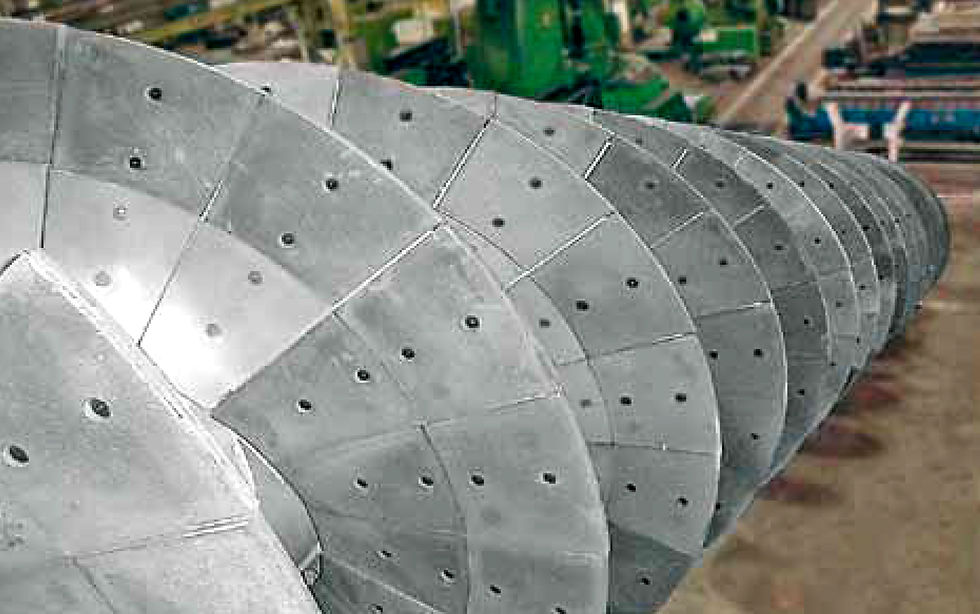
OUR LINING MATERIALS
MINERAL WEAR PROTECTION
ABRESIST fused cast basalt
for protecting plant components when the conveying material which produces friction induced abrasion.
CERAMIC WEAR PROTECTION
KALCOR zirconium corundum
for protecting plant components that are subject to extreme wear and/or high temperatures.
KALOCER high-alumina ceramics
for protecting plant components that are subject to extreme wear and/or temperature conditions. Kalocer is a thin lining for smooth surfaces that is available from 1.5 mm thickness.
METALLIC WEAR PROTECTION
KALCAST
a very hard and wear-resistant chilled iron wear protection for mass-produced components.
KAMETALL
Hard overlay welded steel systems that consist of a tough basic body and the hard overlay welding.
TECHNICAL PLASTIC LINING
KALEN
technical plastic for corrosion-free wear protection which promotes sliding
KALEA
spray-able polyurea-based wear protection for pipes and plant components.
COMPOUND LINING
KALCRET is a cement bonded hard compound for a jointless lining of plant components where high wear and temperature occur. KALCRET allows wear protection of components with complicated geometry. KALPOXY is a compound for the lining of plant components and for repairs, applied by trowel.

BENEFITS
Mineral Wear Protection:
Highly abrasion resistant.
Smooth surface that lasts.
No corrosion.
Ceramic Wear Protection:
Very good abrasion resistance.
Tile, cylindrical or jointless lining.
Temperatures up to 1,000 °C.
Corrosion resistant.
Metallic Wear Protection:
Good resistance against sliding and impact wear.
Thin walls, self-supporting structures
Good thermal shock resistance.
Optimal adaptation to the customer’s requirements.
Technical Plastic Lining:
Excellent slide promotion for many application.
Good resistance against impact wear and Low weight.
Compound Lining:
Highly wear resistant.
Optimal wear protection for every application.
Highly temperature resistant.

WEAR PROTECTED COMPONENTS
Overall, our wear protection solutions reduce operating costs in mining applications by extending service life, reducing personnel costs and minimizing downtime. The table below indicates the lining materials that are typically used to protect different plant components within Mining and Processing plants.
Components Lining Material
Cyclones : ABRESIST, KALCOR, KALOCER, KALSICA, KALMETALL
Fan housings : KALOCER, KALCRET, KALMETALL, KALCAST
Fan rotors : KALOCER, KALMETALL
Gates : KALOCER, KALCOR, KALSICA, KALMETALL, KALCRET
Hydraulic conveyors : ABRESIST, KALMETALL, KALCAST, KALOCER, KALCRET
Nozzles : KALOCER, KALSICA
Pneumatic conveyors : ABRESIST, KALOCER, KALCRET, KALMETALL, KALCRET
Pumps : KALSICA
Separators : ABRESIST, KALOCER, KALSICA, KALMETALL, KALCAST, KALCRET
Transfer stations : ABRESIST, KALEN, KALCERAM
Valves and fittings : KALOCER

BENEFITS OF WEAR & ABRASION PROTECTION
The benefits of our Wear & Abrasion Resistant Linings for Mining and Processing applications may be summarised as follows:
Reduction of wear.
Added value in process security:
Reduction of maintenance costs.
Increasing the lifetime of the system component.
Contribution to the protection of the environment and resources:
Reduction of energy consumption due to reduced friction.
Increase of energy efficiency.

QUALITY WITHOUT COMPROMISE
Backed by a rich tradition characterized by competence and experience as well as durable, quality products. Our wear protection solutions protect industrial plants and equipment reliably against wear due to abrasion and impact. We are committed to quality without compromise with the following initiatives:
Continuous optimization of the properties and manufacturing processes of our materials.
Certified quality control system.
Material testing such as microstructural studies and wear tests according to international standards.
Co-operation with recognized institutes and universities.
Long-term tests for wear resistance.
Customer-specific tests of solutions for the protection against rubbing - and impact wear.

