Following the previous newsletter, this week’s focus is on an additional service offered by the Refractory Anchor Division: A complete range of stud welding systems. A method which has been proven to reduce time and costs, and increase productivity.
Dickinson Industries (Pty) Ltd, and specifically the Refractory Anchors Division is the exclusive distributor of Taylor (UK) and Soyer (Germany) stud welding systems - both leading manufacturers of stud welding equipment. This empowers the Refractory Anchors Division to offer a full range of stud welding systems to its clients. From small hand-held units, to fully automated CNC and robotic methods, adding a distinct competitive edge to the Refractory Anchor Division.

WHAT IS STUD WELDING?
It’s a quick and accurate method of welding a stud to a metal object. During the welding process, an arc is ignited between the face of a stud and the surface of the work piece. Once both surfaces melt, a stud is pressed against the work piece in a level manner and joined together.
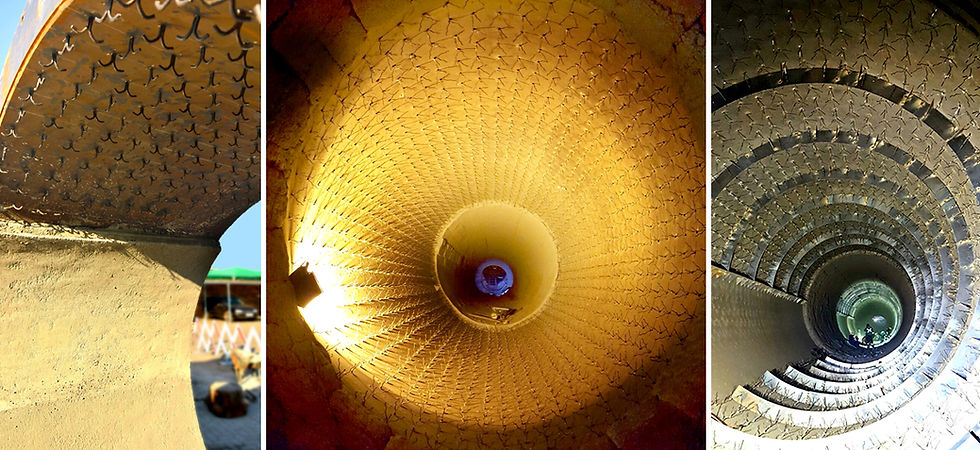
BENEFITS:
Stud welding reduces component handling as it is suitable for especially thin plates, as well as platforms with limited or one-sided access.
Welds are leak and tamper proof.
Since there is no need to punch holes in the parent sheet it eliminates corrosion challenges and the work piece is not weakened.
The end result is a weld joint which is stronger than the stud or parent material.
Improved product design is achieved as reverse marking is eliminated and the area around the studs remains flat and clean.
This technique allows for various elements such as threaded studs, pins and tapped pads to be attached directly to a metal surface.
Through eliminating practices such as drilling, punching, threading, gluing, riveting, screwing or finishing there is a tremendous time and cost saving.
Stud welding is an unmatched efficient system as it entails high automation levels, together with high-speed welding rates, and cost-effective pricing for standard studs.

PRODUCT RANGE:
Capacitor Discharge (CD) Equipment
Capacitor Discharge (CD) Equipment
Drawn Arc (DA) Equipment
Drawn Arc (DA) Equipment
Automatic Systems & Studwelding Pistols
Automatic Systems & Studwelding Pistols
CNC Systems
Desk Type Welding Machines
Accessories

MAJOR APPLICATIONS:
Refractory Anchor Attachment: When compared to the hand welding method it can be said that stud welding is an express method of attaching anchors. The technique eliminates the need for electrodes; eradicating related challenges such as the high volume of fumes generated during hand welding operations. More so, stud welding requires reduced labour, as well as reduced time thereby significantly lowering costs.
Shear Connectors for the Construction Industry: Is an essential part in the design and construction of steel-concrete composite structures. These connectors are stud welded onto the steel skeleton structure of buildings and act as reinforcing components as it locks the support structure to the concrete floor. Ultimately, shear connectors allow for the transfer of horizontal shear forces from the concrete slab to the supporting beams. The use of shear connectors allows for composite construction to be done on a large scale.
Ceramic Fibre Anchors: Refractory Anchors Division provides several systems which are suitable for anchoring ceramic fibre linings across a range of operating temperatures, such as:
Press-On Clip Systems
A wide range of ceramic fibre fixings including: - Fibre-lock Pins - Lock Washers - Spring Clip Washers
Wear Studs:
Are commonly applied in the earth moving industry where excessive machinery wear is experienced. Ideally suited for use on ground engaging equipment in underground and open pit mines; quarries; maintenance shops; steelworks and general ore preparation plants. High chromium and carbon wear studs are welded on surface parts of machinery which are exposed to high abrasion thereby reducing wear and tear, extending machinery service life, and reducing associated maintenance costs.
This system is an intermediate to hard facing and wear plates. It overcomes the shortcomings of conventional welding and further increases benefits when combined with the use of wear plates, resulting in:
High wear and impact resistance - high on-site repair capacity.
Low heat intake, less risk of warping or cracking of the base material. Most base materials which are used in mining can be welded, like hardened fine grain steels (e.g. Hardox 550, XAR). Repeated studding is possible and does not harm.
Studs do not crack if the base material is bent.
The system can be applied on almost every contour.
Very good ratio between wear resistance and weight.

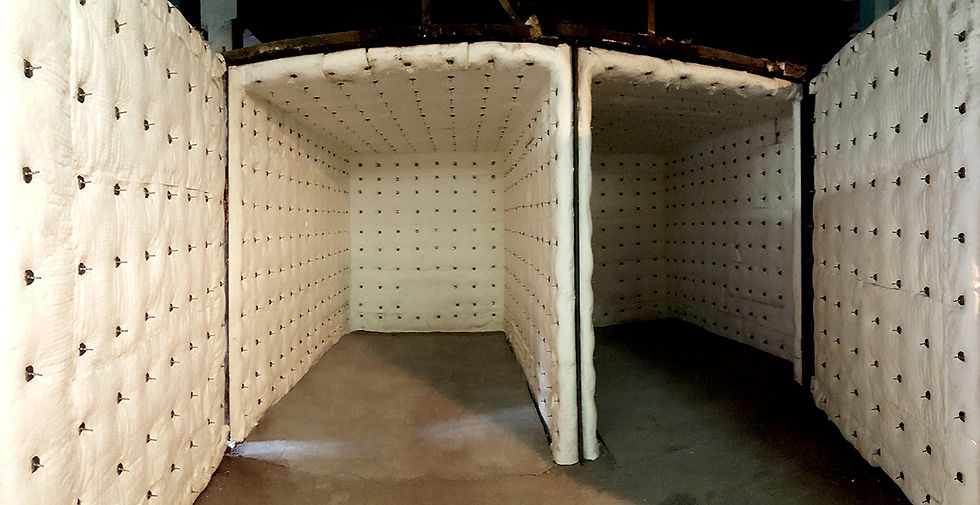