DGC offers highly specialized services for cleaning contaminated and clogged up bulk storage containers in the manufacturing, mining and mineral processing industries.
The services involve the safe and efficient removal of compacted materials, using cutting-edge equipment, which requires no human entry into the storage vessel at any time during the silo cleaning operations. The company adopts a combination of cutting edge silo cleaning techniques, including SiloWhip systems and Cardox CO2 systems. This article will provide a brief overview of both of these techniques that have revolutionised the field of Silo Cleaning.
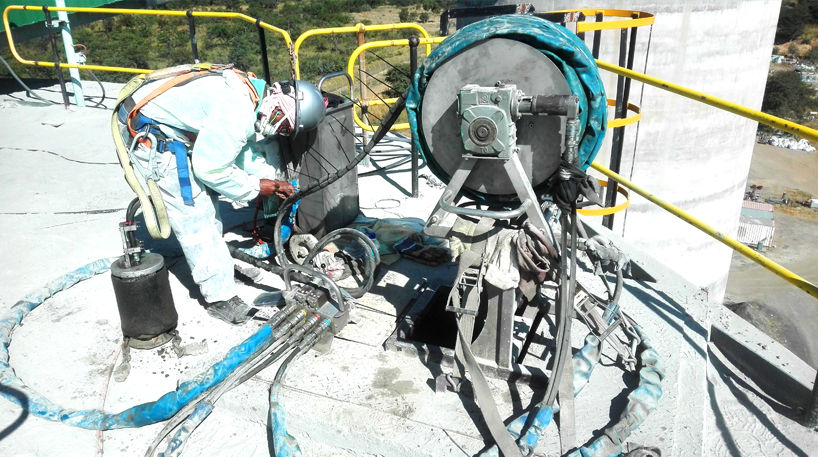
THE CARDOX CO2 SYSTEM
Cardox Systems have a variety of different tubes for specific applications. The Cardox tubes are filled with liquid carbon dioxide - CO2 (exactly the same as a fire extinguisher). When energized by the application of a small electrical charge, a chemical heater instantly converts the liquid carbon dioxide to a gas.
This conversion expands the CO2 volume and builds up pressure inside the tube until the rupture disc at the end of the tube bursts. This releases the CO2 - now 600 times the original volume - through a special discharge nozzle to create a powerful heaving force, at pressures up to 40,000 psi (3,000 bar). All this takes place in milliseconds! This instantaneous build-up in pressure reaches the yielding pressure of the rupture (shear) disc which bursts, releasing a heaving mass of carbon dioxide which breaks the surrounding material. By selecting the thickness of the rupture disc, the power of the tube can be regulated to suit all conditions. After recovering the tube, the heater, washer and rupture disc are replaced, the liquid carbon dioxide is recharged and the tube is ready to be used again.

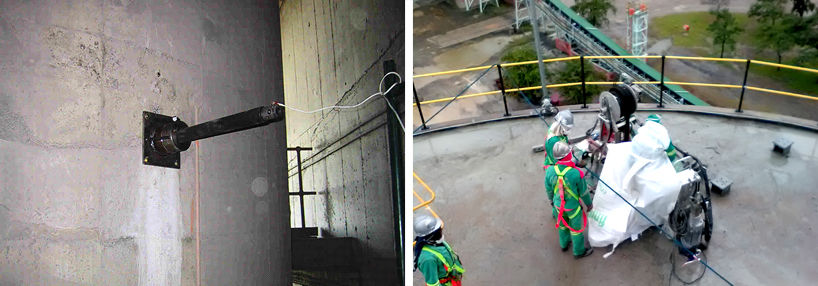
THE SILOWHIP SYSTEM
The SiloWhip System is powered by hydraulics (or pneumatics) and is controlled from the top of the silo; on the outside. The system is composed of a whipping head, boom telescope, hoses and other accessories.
The whipping head is suspended inside the silo and used to efficiently clear material build-ups using the pneumatic or hydraulic driven rotary cutter. The system has 360-degree rotation capabilities and an operating depth of up to 50 meters. A range of cutters are used depending on the type of material a silo contains. Cleared material simply falls to the base of the silo for extraction.
APPLICATIONS
Both techniques are suitable for cleaning bulk storage containers in various industries including special applications like the food industry and combustible materials. The techniques may be used in combination or interchangeably, depending on several application specific factors and client preferences, however their applications can generally be distinguished as follows:
Cardox blasting systems are ideal for clearing blockages at the bottom of the storage vessel; solving problems linked to restricted material flow.
Silowhip systems are ideal for clearing material build-ups on the side walls of a silo, thereby solving problems linked to reduced silo capacity.
BENEFITS
Using these modern techniques allows for significant improvements in the safety profile of silo cleaning activities, notable reductions in the duration of cleaning operations as well as more consistency in the effectiveness of the cleaning activities as follows:
No human-entry into confined spaces.
Flammable, explosive, hazardous or toxic product can be safely removed.
No special safety measures required, only standard operating procedures.
Silo cleaning systems that do not cause damage to facilities or the environment.
The cleaning services are coupled with consulting services, for the adoption of preventative maintenance procedures and the formulation of proper cleaning schedules.