A mineral processing company in Southern Africa’s regular silo cleaning schedules had been disrupted by Covid 19 lockdown restrictions and their operating schedules during the period. One of the company’s mineral concentrate silos with a capacity of over 5 000 ton had gone for a couple of months beyond their regular well-established cleaning cycles.
Consequently, there was severe accumulation of dead material along the sides of the vessel. The silo had build-ups that covered a significant portion of its height, with an estimated thickness of up to 5m at some sections.
Accrual of dead material in bulk storage silos is a well-known phenomenon. This is because bulk solids inside tend to attract moisture, eventually causing material and adhere to the walls of the silo and accumulate. This often results in a number of challenges which include:
Some advantages of DGC’s Silo Cleaning Services when compared to more traditional methods include:
An improved safety profile as operatives do not have to enter the vessel at any point during cleaning process.
Faster clearing of blockages.
More consistent quality of cleaning for the entire vessel.
Minimal manpower requirements.
The following sections will describe the project in more detail.
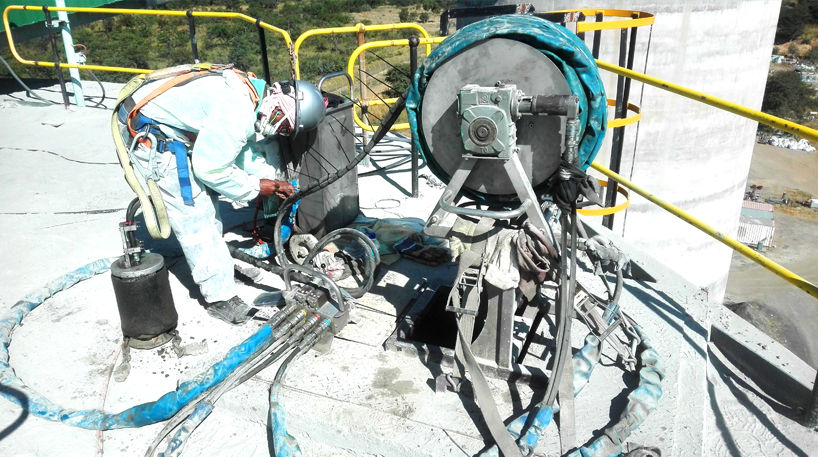

SITE INSPECTIONS
The first port of call for the team during Silo Cleaning Projects is a comprehensive inspection of the silo, as well as its surroundings. This assists the Technicians to get a better understanding of the nature and quantity of build-up. Thereafter the team would be in a position to recommend the most appropriate silo cleaning technique.
DGC’s Silo Cleaning Services specialize in two techniques:
SILO WHIP: consists of a pneumatic or hydraulic driven rotary cutter with a 360 degree rotation capability, and an operating depth of up to 50m. The system is controlled from the top of the silo’s roof. Operators guide the whip as it cuts through dead material along silo walls. Cleared material falls to the base of the silo and is extracted normally.
CARDOX BLASTS: consists of cardox tubes which are filled with liquid carbon dioxide. Reusable and pluggable openings are then strategically drilled on the shell to ensure that the tubes are positioned within the accumulated dead material. Once energized by the application of a small electrical charge, a chemical heater instantly converts the liquid carbon dioxide to a gas, expanding it and building up pressure until a rapture disk at the end of the tube bursts. This instantly releases the CO2, now 600 times its original volume, creating a heaving force that shatters dead material. Cleared material also falls to the base of the silo and is extracted normally.


EXECUTION OF SILO CLEANING TASKS
In the case of the Mineral Processing Company the silo cleaning team decided to use the Silo Whip technique. This involved establishing, two 12 hour shifts with minimal manning levels to operate the equipment. Throughout the cleaning process the silo’s extraction conveyor belt was run in bypass mode to handle cleared material. After 6 shifts, a significant amount of progress had been made and a large amount of the dead material had been cleared out. Unfortunately cleaning operations had to be stopped when the short maintenance window lapsed and the plant had to be put back online. The client was however very happy with the progress that was achieved within the constrained time.
